Fujian Refractories Unshaped Ingredients and Mixed Packaging Production Line
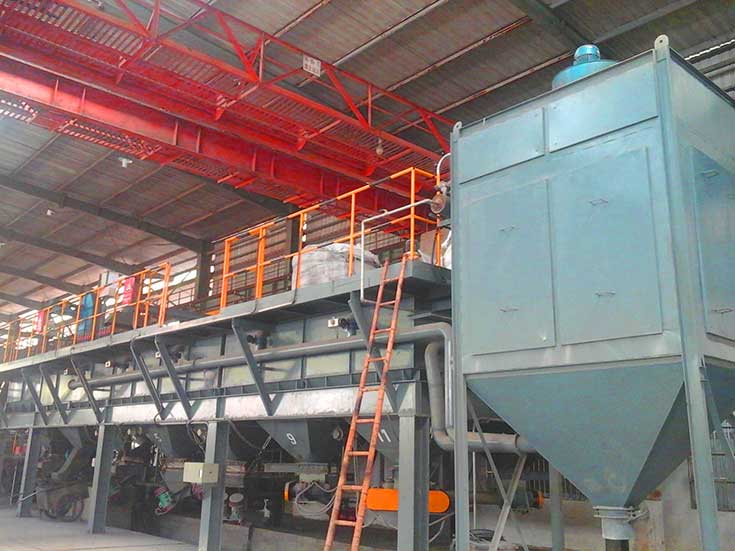
一、Composition of the equipment for the production line of amorphous burden and mixed packaging of refractory materials:
According to the actual production needs of users, our company designs a mixed packaging production line of refractory amorphous ingredients. The main equipments include raw material warehouse, ingredient system, mixing system, packaging equipment, dust treatment equipment, control system and so on.
1. Raw material warehouse: Manual travelling stock is combined with upstream crushing and grading production line chute feed. Wire mesh is installed in hatch to filter impurities, and bulkhead vibrator is added according to the characteristics of raw materials. Each warehouse is equipped with an open repair door to facilitate material exchange and cleaning. All silos are equipped with manual repair valves to facilitate equipment maintenance. Each silo has an automatic control opening and closing dust collecting seal, and the dust collecting air door opens when feeding. The warehouse is equipped with a weighing level meter, which can display the warehouse capacity in real time through the screen, and send out prompt signal for feeding in time. The warehouse capacity can be predicted according to the prescription requirements, and the feeding of relative kinds of materials can be judged and prompted. Printable report of raw material consumption
2. Batching system: 10 sets of vibration feeding mechanism provide granular raw material feeding, 4 sets of double-power screw feeding machine provide powder raw material fast and slow feeding. The weighing unit of the batching trolley measures all kinds of materials separately, completes the automatic batching of various formulas, the trolley is equipped with pulse dust collector, and the batching process realizes the fully closed work. The batching process is conveyed to mixing by a sealed lifting trolley. In the mixer, then enter the mixing process, the middle mixing and the ingredients of each section can be interpenetrated.
3. Mixing system: The mixer has an automatic discharging door. After mixing according to the process requirements, the discharging door of the mixer opens, and the materials are automatically discharged into the packaging transfer bin according to the process requirements and enter the next packaging process.
4. Packaging equipment: According to the user equipped with a warehouse (with movable hatch door) with a volume of not less than 1.7m, using two automatic packing scales of mixture materials; using manual bagging, automatic weighing, automatic packaging; with the function of accumulating packages, accumulating weights, batch packaging, equipped with U232 and 485 interfaces, can communicate with computers and printers.
5. Dust handling system: The whole system is closed, and dust collecting and processing are carried out by setting corresponding dust collecting outlets and automatic air lock valves at feeding, proportioning, feeding, mixing and packaging interfaces, so as to maintain the environmental protection operation of the whole system. The mixing and packaging station has a silo-type dust collector separately for dust collection and treatment. The collected materials are directly added to the packaging silo to ensure the formulation and accuracy of the mixture.
6. Control system: An independent control room is set up to control and operate the whole batching and packaging system. The omni-directional control system equipment is designed, including: PC monitoring system: industrial computer + WINCC PC software is installed in the control room to realize the monitoring of the whole system, formula setting, system parameters setting, real-time alarm, batching process data report. Siemens S7-300 Master Controller: As the master station of the system, it can complete the measurement and control of the whole system, complete the communication with the host computer, and has a very strong expansion function. Execution system: It mainly includes 10 sets of variable frequency speed regulating vibration feeding mechanism, 4 sets of variable frequency speed regulating screw feeding machine, movable belt conveyor, lifting bucket car, mixer, solenoid valve and cylinder, etc. (4) On-site detection system: weighing sensor, proximity switch, etc. Manual operating system: Complete the corresponding manual operation function of the system. The control system includes: (1) the batching subsystem: the control of the subsystem can be completed in the control room or by the batching car. According to the instructions of the mixer, each kind of granular material and powder material is fed and weighed by the vibration feeding mechanism and the speed regulating screw feeding machine according to the prescription requirements until the ingredient is finished. After the ingredient is finished, the material in the cart is imported into the lifting hopper through a movable conveyor belt, and is transported to the mixer by the lifting hopper truck, entering the mixing process, and the ingredient system enters the next ingredient process. 。 A mobile trolley is set up on the batching production line, which can collect materials directly under each warehouse, so as to facilitate the replacement of raw materials for cleaning construction. (2) Mixing subsystem: mixer feeding is completed, mixing time is set according to the system, mixing is completed according to the process requirements, the system sends out discharge instructions, the mixer discharge outlet cylinder action, opening the discharge outlet to start discharging, according to the set time discharging is completed, the cylinder reverse work discharging door closes, and then sends out feeding instructions, the charging belt starts to work, and enters the next mixing. Cycle. The packing station starts the packing process according to the actual situation. (3) Dust treatment: dust collection and treatment are carried out in the transportation and mixing links of the system. The whole batching system is controlled by PLC. The dust collector is only activated when the equipment is running. When the equipment stops, the relevant dust collector pipeline or the whole dust collector is closed.
二.Operating flow of the production line of amorphous burden and mixed packaging for refractory materials:
1. Production start-up:
The operating table is equipped with manual control buttons and indicator lights of various process links, as well as start buttons. Operators can press the button on the panel of the operating table or click the start button on the screen directly with the mouse, which can start the production line manually or automatically.
2. Formulation management:
Before each production, we can set up the formula to input the ingredients and distribute the required raw materials proportionally (or we can use the default method, that is, we still use the formula of the last time). Provide data basis for automatic feeding.
3. Dynamic measurement of production process:
At the same time of production start-up, the PLC sends the dynamic measurement start-up signal to the weighing instrument. The instrument begins to collect and display the weight of each link, and adopts the strategy of fast feeding and slow feeding in different weighing stages to improve both efficiency and measurement accuracy. When the target value is reached, the stop measurement signal is output, and the feeder is controlled by PLC to stop working. At the same time, the movement from discharging to receiving belt is completed, and the measuring instrument automatically clears and peels.
4. Data storage:
At the end of this batching, the upper computer (computer) can store the actual data, and make certain accuracy analysis according to the requirements, and generate various reports for production statistics and management.
5. Report printing:
Print the required reports online or offline as required, such as daily output of finished products, consumption of raw materials, etc.
三、The main configurations of the production line of amorphous ingredients and mixed packaging for refractory materials:
The electrical appliances and components of the company's equipment are imported components with long service life and high stability.
Cylinder: Yadeke, Taiwan, Solenoid Valve: Forstow, Germany, Inverter Mitsubishi, Japan
Inverter: Mitsubishi, Japan
Weighing sensor: AVIC electric measurement;
Instrument: Gemman, Canada
Solenoid Valve: Festo, Germany
四.Equipment parameters of the production line of amorphous proportioning and mixed packaging of refractory materials:
1. Accuracy: The accuracy of proportioning is 0.2%. The weighing accuracy of each material is 0.2%. The proportioning speed is 3-5 minutes per time (from the dispatch of the proportioning instruction, the proportioning metering begins in 2-3 minutes and the proportioning ends in 1.5-2 minutes until the material is fully conveyed to the mixer).
2. Production capacity: 30-50 t/h for each feeder and 10-18 t/h for the batching system.
五.Fire Material Unshaped Ingredients and Mixed Packaging Production Line Company Services:
1. Quality Assurance: The quality of the whole system and equipment shall be guaranteed in three packages with a period of one year (excluding vulnerable parts).
2. Construction: The contractor is responsible for the on-site installation and commissioning, and the customizer is responsible for the lifting required for the on-site installation, including power supply and socket, and assigns a field coordination commander.
3. Acceptance and acceptance: After installation and commissioning are completed, the supplier's personnel can leave the site only after acceptance and acceptance by the buyer is qualified.
4. After-sales service: If problems are found in the system operation within one year, the supplier dispatches staff to the site within 24 hours. In the next three years, if there are problems that users can't handle, the supplier dispatches free technical support to the demander.
5. Technical undertakings: Within 10 days after the signing of the contract, the Contractor shall provide the layouts of the process line grooves, pile loads, the general layout of the system, as well as the production and processing drawings of silos and steel structures (self-made by the demander). Free training and guidance for the personnel of the demander's post, including operation, commissioning and equipment maintenance.
- Last:请返回Next
- Next:Henan Compound Fertilizer Fully Automatic Packaging and High-level Palletizing Production
【Related Product】
- Full-automatic Packaging Machin
- Semi-automatic valve bag packin
- Semi automatic powder packaging
- SW-ATF-180 Fully Automatic Pack
- Semi-automatic Ton bag Packing
- Double hopper granule packing m
- Single hopper packing machine
- Semi-automatic packing machine